Introduction: Working Sonic Screwdriver - Version 3.0
This is my third rendition of a sonic screwdriver complete with working sound and a TVbgone circuit.
Now that is over, let us have some fun.
Some features:
- A true-to-series sound
- A tvbgone clone circuit. It turns almost any tv on or off within a few seconds with the press of a button
- A UV light in the front to reveal invisible ink
- AA battery for simple replacement
- Feels real: The prop is made mainly from metal and glass, giving it a solid feel
- Accident resistant: one of my earlier version was broken by my nephew's head. This version is far more robust and can be dropped from a reasonable height with minimal damage (I don't recommend it, but when you are saving the universe....)
- Simple to construct: In theory the prop can be made with a hand drill, hack saw, some sand paper, a soldering iron and JB weld epoxy. I use a few more advanced processes but the entire device can come together in a weekend (or 5 in one weekend as I have done)
- Varied lighting effects. There are three colors of LED's in the front of the sonic that vary the quality of the light greatly giving a blue hue in front and a green hue when viewed from the side.
- Easily customizable. The colors of the LEDs and glass bead on the front are easy to exchange and since the device is made from plumbing parts there are a wide array of possibilities for add-ons or changes.
Step 1: Materials
Most of the materials required for this project can be found at almost any home improvement store, craft store or can be ordered online
Materials Required:
Hardware Store
1-Black Steel Pipe Nipple 1/2” x 5”
1-Flare cap LFA-342
6 Inches - Clear vinyl tubing, 3/4” OD
1-1/2" Female Copper Threaded Adapter
1- 5/8" Flare Nut
At least 1" of 1/2" copper pipe
1 - 1/2" PVC coupling
all of the above may be found at almost any hardware store in the plumbing section
Craft Store:
1-Floral Decorative Gem, Found At Michel's or other craft stores. Choose a color
Electronics:
2 - Attiny85 Microcontrollers
2 super-bright LED, 3mm. They may be different colors. A self cycling RGB led would also be cool (If there is interest I should be able to add control of an RGB led to the sound circuit)
1 long range IR led, 3mm or 5mm
1 UV Led, 3mm or 5mm
1 Piezo SpeakerPiezo Speaker, less than .5 inch di (working on finding a new speaker and adding a transformer)
Thin gauge stranded wire, 22-28ga. Thinner is more flexible and will fit better in the handle
1 Bipolar NPN transistor
1 10uf electrolytic capacitor. It needs to be small
1 100 ohm through hole resistor
Heat Shrink Tubing
1 button. I use one I bought on ebay, though in theory any small momentary push button that is less than .6 inches should work.
.1" pitch perfboard
Tools:
Pipe Cutter
Pipe Deburring tool (a razor blade or file will work as well)
A needle file
Drill Press Vise (Harbor Freight sells them for $12)
Drill Press (If you do not have a drill press, all of the holes may be drilled with a power or hand drill, though it is harder to accomplish)
Fine grit sandpaper (I only used 320 grit wet/dry sandpaper. Other grits will work as well)
Pencil
Some form of razor blade (I use the snap off retractable blade form)
1/8" drill bit
5/16" drill bit (smaller diameter of button)
25/64" pilot point drill bit (larger diameter of button)
butane torch
flux core solder
water based plumbing flux
brick or heat resistant surface
hacksaw
hose clamp
JB Weld
Hot glue gun
soldering iron
Step 2: The Front End Part One: Cutting the Connector
Between the female copper connecter and the short flare nut exists a small piece of 1/2 inch copper pipe.
- Measure 1" down from the end of the 1/2" Copper pipe, mark with a nail, sharpie or pencil
- Cut off this section using a standard pipe cutter
- Deburr the inside of the pipe using a file, deburring tool, a razor blade or sand paper until it is no longer sharp.
Step 3: The Front End Part Two: Drilling the Connector
Without any holes in the device for sound to escape the sonic sounds muted and weak. I solved this problem by drilling 6 holes in the copper connector piece right where the speaker lives.
- Measure 1/2" down from one end of the copper connector and mark it with a pencil, sharpie, razor blade or nail, this should be center
- Use the pipe cutter to very gently scribe the measurement all the way around the copper pipe
- Keeping track of the scribed mark, insert the connecting piece into the adapter until it reaches the inner ledge
- Place the assembly into a drill press vice with one of the flats on the female adapter touching the bottom of the vise
- With an 1/8th inch drill bit in a drill press, drill through both sides of the connector using the scribed mark as a guide. Alternatively you may drill with a hand drill if you only drill through 1 side of the connector at a time or trust your judgement of perpendicular.
- Rotate the assembly in the vise until a new flat on the female adapter is along the bottom of the vise. Make sure not to mess up the alignment between the copper pipe and the adapter (I marked them with sharpie to remember)
- Continue as before until there are 6 holes in the copper pipe
- Deburr the copper pipe with a deburring tool, razor blade, sand paper or a file
- Sand the exterior of the copper pipe in preparation for soldering
Step 4: The Front End Part Three: Soldering the Pipe and Female Adapter
Once sanded the pieces are almost ready to solder together.
If you are not able to solder the joints together or do not want to JB weld may be exchanged for the solder and no torch used, it just takes longer to set. Let the epoxy cure entirely before moving on.
- Prepare any fire safety materials needed such as a bucket of water, some wet rags and a fire extinguisher
- Sand the interior of the female adapter piece and the exterior of the copper pipe to ensure a good connection
- Add some water based plumbing flux to the bottom half of the connecting piece and the inside of the female adapter, then slide them together.
- Ready a butane torch to light, place the setup on a fireproof surface such as a brick
- Light the butane torch and adjust for a small blue cone of fire
- Gently start heating the copper female adapter side of the setup by passing the torch back and forth over the joint
- To test if the setup is hot enough pull the flame to one side of the joint and touch the solder to the flameless side, just where the two pieces meet If the solder melts and begins to flow continue adding solder until it rings the joint and creates a solid connection.
- The solder will flow towards the heat of the torch If the solder does not flow, continue gently heating the joint and testing until it does
- Let the setup cool on the brick while preparing the next step
Step 5: The Front End Part Four: Adding the Flare Nut Front End
The very front end of my design involves a brass flare nut to give it some character. The flare nut is soldered to the copper connector as before and will house the lights and speaker for the sonic screwdriver.
- While the female adapter and copper pipe connector cool cut 2 lengths of 1/2" copper pipe to 3/4" length just as before.These pieces will create a jig to hold everything together while the second part is soldered. (if JB weld is being used the jig piece does not need to be used.)
- Sand the inside of the flare nut where it will connect to the copper pipe
- Place the short length of copper pipe on the brick ready to be soldered.
- Place the short flare nut on top of the copper pipe with the hexed end down
- Brush flux on the inside of the flare nut where the new pipe will be placed as can be seen in the photos
- Before you touch the female adapter piece make sure it is cool by holding your hand a distance away and closing that distance, feeling for heat, until you can quickly touch the part. If it is still too hot, wait until it is cool.
- Once the female adapter piece is cool, sand the oxidation off the copper pipe to ensure a good connection, then brush flux over the free end of the connector
- Slide the connector piece into the flare nut, lining up the hexes on the flare nut and female adapter Following the same steps to solder as before but with the flare nut as the target, solder the flare nut to the prior assembly
- Wait for the assembly to cool
- The copper jig pieces will have been fused to the flare nut in the soldering process, using a pair of pliers break them out
- Rinse the entire part with water to remove the flux.
Step 6: The Handle Part 1: Drilling and Cleaning the Steel Pipe
There are two modifications that have to happen to the 1/2" by 5" black steel pipe for this project: Drilling a clearance hole for the button and cleaning the oil/paint residue from the exterior of the pipe.
To drill the hole:
- tape a piece of paper around the steel pipe near one end
- measure 3/4" from the top of the pipe and mark
- screw on the female adapter to the end with the paper
- mark the center of one of the faces of the adapter on the previously drawn mark
- Set the pipe into a drill press vise with the mark facing up. Use the adapter to square the face to the vise
- Place an 1/8th inch drill bit into the drill press, drill through one side of the pipe along the previously made mark
- Place a 5/16"drill bit into the drill press, repeat drilling process. A bit of cutting oil will help
- Remove the pipe from the drill press vise, remove the adapter and the piece of paper
- Use a pipe deburring tool and/or a file to remove the burr from the inside and outside of the pipe where you drilled
To clean the pipe:
- Sand the entire exterior of the pipe to remove oil and paint residue.
- To remove chips from the threads of the pipe I use a car battery terminal cleaner.
- Wash the pipe with a degreaser and thoroughly dry it
Step 7: The Handle Part 2: Cutting the PVC
The piece between the grip and the female adapter holds the button and is made from a 1/2" pvc coupling.
- Measure 1/2" down from each end of the pvc coupling and mark with a pencil or pen
- Place a pipe clamp over the pvc coupling, aligned with one of the previously made marks
- Use a hacksaw to cut through the pvc coupling using the pipe clamp as a guide
- The width of the hacksaw blade should cut the pvc coupling almost perfectly in half leaving two 3/4 inch sections
- Deburr the inside of the pvc pipe (there is a groove in the middle of the coupling that will get in the way later if not removed)
- Sand and clean the piece of PVC
Step 8: The Handle Part 3: Drilling the PVC
To accommodate the button I have chosen the PVC needs to be drilled through with one size and countersunk with a slightly larger size.
- Divide the piece of PVC in half with a pencil mark
- Using either a centerpunch or a razor blade, make an indentation at the mark
- Place the PVC piece into a drill press vise and set up the drill press to drill an 1/8th inch hole
- Drill through 1 side of the PVC with the 1/8th inch drill bit.
- Change to a 25/64" pilot point drill bit. Dewalt sells very nice ones.
- Countersink a small amount into the PVC over the previously made hole
- Change to a 5/16" drill bit and drill through one side of the PVC
- Deburr and clean the PVC
- Test fit the PVC over the steel pipe to make sure the holes align well
- Test to see if the button fits, if it does you are golden
Step 9: The Handle Part 4: Adding the Grip
Some setup:
Place the PVC coupling on the steel pipe and line it up with the hole in the pipe
Square and clean the end of the vinyl tubing with a razor blade
From the end opposite the hole:
- Slide the 3/4 inch vinyl tube over the steel pipe until it meets the PVC coupling. Oil or soap may help but are not needed. This step is the most time consuming as it is a very tight fit
- Measure 1/2" up from the bottom of the steel pipe and mark it
- Place a hose clamp over the vinyl tubing and use it as a guide to cut all the way around the tube in several passes
- Clean up the edges
- The flare cap should be able to reach the tube when it is screwed on
Step 10: The Bottom Cap
The flare cap that will cap the bottom of the sonic screwdriver needs a battery terminal to provide power to the setup.
- Sand the interior of the flare cap to prepare for soldering
- Place the flare cap on a brick or other soldering surface
- Place the spring battery terminal into the flare cap as evenly as possible
- Heat the flare cap with a torch until a piece of solder touched to the corner of the battery terminal melts and forms a small bead
- Solder each of the corners of the battery terminal to the flare cap
- Allow the cap to cool
- Rinse the cap to remove the soldering residue
- If desired a 15.8x2.5mm or similar Oring may be placed into the flare cap at this time. The o-ring gives a better feel to closing the sonic as well as providing some water resistance but it has a tendency to fall out. To help prevent that it may be glued in place though that is not 100% effective.
Step 11: Test Assemble the Hardware
If all went well the sonic should resemble the above photographs. It is now ready for the electronics.
Step 12: The Electronics Part 1: Setting Up the Development Enviroment
Before the either circuit can be programmed the environment must be set up
Copy and install the arduino software (windowsMac)
Download the library.zip file attached to this step (from here)
This following section is taken from the readme file included with the library:
Ensure the Arduino IDE is NOT running.
* Download the Arduino-Tiny archive (ZIP-file).
* Locate the Arduino Sketch folder. This is the folder where the Arduino IDE stores Sketches.
* Ensure the "hardware" folder exists under the Arduino Sketch folder. For example, if the Arduino Sketch folder is...
C:\Projects\Arduino\
Ensure this folder exists...
C:\Projects\Arduino\hardware\
* Extract the contents of the archive into the "hardware" folder. For example, if the Arduino Sketch folder is...
C:\Projects\Arduino
After extracting, the following files / folders should exist...
C:\Projects\Arduino\hardware\tiny\license.txt C:\Projects\Arduino\hardware\tiny\Prospective Boards.txt C:\Projects\Arduino\hardware\tiny\README C:\Projects\Arduino\hardware\tiny\bootloaders\ C:\Projects\Arduino\hardware\tiny\cores\
The following folder should contain the source files for the Arduino-Tiny core...
C:\Projects\Arduino\hardware\tiny\cores\tiny\
* Create a new file named "boards.txt" in the tiny directory. Following from the examples above, the file would be here...
C:\Projects\Arduino\hardware\tiny\boards.txt
* Open the "boards.txt" file and the "Prospective Boards.txt" file using your favourite text editor.
* Copy board entries of interest from "Prospective Boards.txt" to "boards.txt" (or copy the entire contents of "Prospective Boards.txt" to "boards.txt"). Board entries are delineated by a long line of pound-signs.
* In the "boards.txt" file, change the "upload.using" entries to the appropriate value for your setup.
* Save and close "boards.txt". Close "Prospective Boards.txt".
* Start the Arduino IDE and ensure the new boards of interest are listed under the [Tools] [Board] menu...
"ATtiny84 @ 16 MHz (external crystal; 4.3 V BOD)" "ATtiny85 @ 8 MHz (internal oscillator; BOD disabled)" etcetera
You are now ready to use Arduino-Tiny!
Attachments
Step 13: The Electronics Part 1a: Setting Up the Development Enviroment 2
The arduino mega now needs set up to program. This step should be quite easy.
The arduino mega's drivers need installed. Arduino has a lovely section of instructions detailing exactly this here.
I can write a set of instructions on how to set up the arduino if requested but I thought I would cut a bit of length here.
- Once the arduino mega is installed open the arduino enviroment.
- Open the ArduinoIsp example
- Select the correct serial port
- change the board to the arduino mega 2560
- click the upload button
- If all goes smoothly and arduino says upload complete you are ready for the next step
Step 14: The Electronics Part 2: Breadboarding the Sound Chip
Before anything can happen with the circuitry in this project it is advisable to put the chips on a breadboard to program and test them. They follow very simple schematics as shown above. I am going to show how to program the attiny with an arduino mega 2560. The process is similar for different programmers with a slightly different wiring setup.
If you would like to use an arduino uno on this part of the project, check step 7 of
https://www.instructables.com/id/Working-Sonic-Scre...
To program the sound chip:
- Place the attiny in the breadboard with the dot facing the edge of the board
- Connect pin 7 of the attiny to pin 52 of the mega
- Connect pin 6 of the attiny to pin 50 of the mega
- Connect pin 5 of the attiny to pin 51 of the mega
- Connect pin 1 of the attiny to pin 53 of the mega
- Connect pin 4 of the attiny to GND on the mega
- Connect pin 8 of the attiny to VCC on the mega
- plug the mega into a computer with a usb to serial adapter
- open the arduino programming enviroment
- Open the tools drop down, hover over boards and select the optiboot attiny85
- Check the serial port, it should be active. If there is more than one, disconnect the arduino, watch which one disappears, then plug it back in. Whichever one changes is the port the arduino is on, select that one. Write this value down for the next step.
- If all seems good click the burn bootloader button and wait for the upload. If there are any errors check connections. Sometimes you need to reconnect everything quickly.
- open the sonic screwdriverattinyfinal file in the arduino environment (file is attached)
- if everything was set up properly in the previous step you should be able to click the upload using programmer button (cntrl+shift+U)
- When the file is done uploading connect the positive lead of a 10uF capacitor to pin 3 as shown in the image above.
- There will be two errors about PAGEL files, ignore them.
- If there are any other errors other check the connections, the programmer, and make sure the COM port is active.
- Connect the negative end of the capacitor to the positive end of the piezo speaker and the negative leg of the speaker to ground (pin 4 may be used.)
- A sound should result. If there is no sound check the connections
- Mark the sound circuit somehow (I use tape) and set it aside.
Attachments
Step 15: The Electronics Part 3: Breadboarding the TVBGone Clone
To program the TVBgone the circuit setup is the exact same as the sound chip. Follow the previous step until it gets to opening the sound file. Instead we will be using a different program.
I am using avrdude to program a hex code from adafruit onto the attiny.
- Download avrdude and install
- download the attached tvbgone.hex file and save it to C:/users/YOURNAME/tvbgone.hex
- open command prompt (start, search command prompt)
- type avrdude into command prompt, a bunch of text should show up, if not check your installation
- if you are using the same setup as I am then you may copy the following text verbatim into comand prompt
avrdude -c avrisp -p attiny85 -b 19200 -P COM3 -U lfuse:w:0xe2:m -U hfuse:w:0xdf:m -U efuse:w:0xff:m -U flash:w:tvbgone.hex
- From step 1 of the electronics section the COM port may be different, just change the number above
- If you are using a different programmer follow the steps outlined here
- once the text is entered hit enter and a bunch of text will appear. At the end it should say avrdude done Thank you! if not check connections, your com port and if the text is typed in correctly.
- Unplug the positive wire from the programmer to the attiny85
- Connect pin 1 (reset) to the positive source (pin 8)
- Connect a 100 ohm resistor to pin 5 of the attiny
- connect the middle pin of an NPN transistor to the other end of the resistor
- connect the right leg of the transistor to ground (pin 4)
- connect the left leg of the transistor to the negative leg of an IR LED
- Connect the positive leg of the IR led to the power (pin 4 or 5)
- Place the circuit in front of a television and replace the positive wire. Within a few seconds the tv should shut off
- An LED connected between pin 7 and ground should flash when the power is on.
- If nothing is happening test connections as well as the code typed in earlier.
- If all is working set the attiny aside with the sound circuit, marked differently. (again, tape is a good idea, preferably a different color)
Step 16: Building the Circuit Part One: Perfboard and IR Circuits
Now begins the final assembly of the microcontrollers.
- On the perfboard count 6 holes from the edge. Run a razor blade down the center of this 6th hole a few times to score the break
- Snap along the previously scored line
- Count 6 holes from one end of the perfboard rectangle you have created, score and snap
- You should have a 5x5 hole piece of perfboard that should fit an attiny85 with a set of holes to the LEFT and bottom (previously I said right, and that is wrong.)
- Now take out the IR circuit
- Filp it over and break off pins 2,3,6 and 7 (the middle pins). You should now have a four legged microchip
- Place this chip into the perfboard with a row of holes to the right and below.
- fold over pins 1, 4 and 8 as shown in the picture
- If all went well it is time to move onto the sound circuit.
Step 17: Building the Circuit Part 2: Sound Circuit
Let us continue on this journey through microcontrollers with one built to produce sound. This microcontroller is labeled with a pink star to denote it's amazing qualities.
The first thing to be done with this new, awesome chip is to flip it over and remove some useless legs.
Clip off legs 2 and 5-7 as shown in the picture, they will not be needed.
Once that is done bend legs 1 and 8 together and quickly solder them to form a secure connection.
Flip the perfboard with the IR chip upside down with pin 1 (the one with the dot next to it) closest to you
Place the new chip ontop of the IR chip setup lined up with the empty set of holes on the left as shown in the image and the sets of pin 1 and 8 on each chip line up.
Solder the sets of pin 1 and 8 together and you are ready for the next step.
Step 18: Building the Circuit Part 3: Adding the Capacitor
Let us add a capacitor to the mix for fun. It sits on the same side as the audio circuit with the long leg bent and attached to pin 3 of the sound chip with a smidgen of solder.
Once that mess is done flip the whole thing over and bend the legs of the capacitor to the right. Solder a long stranded wire(2-3 inches) (mine are blue) to the short leg of the capacitor, keep track of it as the wire to connect to the speaker, and clip the legs of the capacitor so they do not short circuit, cause problems and lead to the premature death of your sonic.
Step 19: Building the Circuit Part 4: Adding the Transistor and Resistor
Now to add some more discrete components to make the tvbgone circuit work as it should.
The first up is an NPN transistor that is bent as shown in the first image.
It happily lives behind the sound circuit with the flat face away from the chip.
Now for the resistor, trim one leg of it so that it is only about 1/16th of an inch long.
The long end of the resistor wraps around the middle leg of the transistor and the short leg of the transistor connects to pin 4 of the TVB gone circuit as can be seen in the 4th image above.
A new wire (2-3 inches) (mine are white) is connected to the leg of the transistor nearest the blue wire.
This whole mess is soldered together at the new connection points and the extra legs removed by clipping with a pair of wire snips. If the legs are not clipped gremlins shall enter your sonic and make it hiccup at the most inopportune moments, from something as simple as locking the door you are trying to open to creating a delta wave of doom and gloom, eradicating the nearest living species.
Step 20: Building the Circuit Part 4: the Negative Wires
Discrete components are done for the moment and we can move back to simple wires (with somewhat convoluted path)
Take two long black wires (2-3 inches) and connect them to the remaining pin on the transistor as well as pin 4 on the top circuit. Now take a short black wire (1 inch) and connect it to the same location and solder that whole mess together.
Now take the other end of the short wire and connect it to the bit of pin 4 on the audio circuit (you can reach it from the IR circuit side). The route the wires take can be seen in the pictures above.
One wire goes out the top of the circuit and the other out the bottom.
Step 21: Building the Circuit Part 5: the Positive Wires
Now for the last set of wires before the microcontrollers can be sealed up. Two long red wires (2-3 inches) are connected to that pin 1 and 8 mess at the front of both microcontrollers with one wire going out the top and bottom of the circuit to connect to the leds and button respectively. Please use solder on this connection or your circuit will most likely disintegrate violently, tear a hole in space and time, and generally lead to not very good things.
Step 22: Building the Circuit Part 6: Insulation
Insulation is up.
I start with hot glue to secure the connections. See the third picture for which direction the wires go, white, blue, red and black out the same side as the capacitor, and red and black out the other.
A little bit of hot glue goes a long way here as the whole thing will be shrinkwrapped next.
Take a piece of heat shrink tubing that is about the right side for the circuit.(trim it to length) If it is too small take a pair of long nose pliers, slip them inside the tube and expand the pliers to resize the piece of tubing.
Slide the heat shrink tubing over one set of wires and over the entire circuit. Once it is in place take a lighter and gently heat the tubing until it conforms to the shape of the circuit.
Add a bit of hot glue into both ends of the circuit to completely waterproof it.
The only steps left are to connect the LEDS, speaker, button and batteries.
Step 23: Step 23: Final Electronics Intro
The sonic screwdriver will start doing things very soon, I promise.
First off we need a few parts as seen in the picture above. Gather:
One of the crazy circuit things you just made
One UV LED (if you are using it)
One blue and one green LED (or whatever colors you are working with)
A small speaker less than .5 inches in diameter
One pushbutton
Step 24: Step 24: Final Electronics, LED Assembly
The first bit you need to work on is the LED assembly.
This method is a bit sloppy but works very well for a sealed project:
Take all four LEDs and put them on your work surface
Wrap the positive legs(longer ones) of the IR and UV leds together
Take the green LED, wrap the positive leg around the positive leg of the UV led and the negative leg around the negative leg of the UV LED
Do the same for the blue led on the other side of the UV led as shown above.
Wrap the red wire from the microcontroller top (the side with 4 wires) around this central mass of positive legs
Wrap the white wire around the free leg of the IR LED (it is also the negative leg if you are concerned)
Wrap a 2-3 inch length of black wire around the negative legs of the UV, green and blue leds. It is NOT the same black wire that comes out of the microcontroller mess.
Now. Test everything. First connect the black wire from the 4 wire microcontroller side to the black wire you just added and connect the red and black wires from the microcontroller side with 2 wires to the + and - of a 3v source (two AA batteries end to end) to make sure all the LEDS light up. Also put it in front of a tv and make sure the tv shuts off.
Solder that mess together, being careful not to heat the LEDS too much or they will fail
Snip off the extra length of each leg up to the ball of solder
Now. Test it again.
Hot glue insulate the whole mess as shown in the photo above.
One more time, test this whole mess.
Step 25: Step 25: Final Electronics, the Speaker
Without the speaker the sonic screwdriver is just about useless. Something about the word sonic....
Take the blue wire from the microcontroller and wrap it around the positive pin of the speaker (it should have a plus mark somewhere or something) There might be a sticker on the speaker, remove it.
Wrap the black wire from the 4 wire side of the microcontroller setup (Trimmed to an inch and a half or so) and the black wire from the light assembly around the other pin of the speaker.
Test the whole mess by connecting the red and black wires to the two batteries as before. If it all works:
Solder the three wrapped wires to the speaker and cover the connections with hot glue.
Step 26: Step 26: Assembling Every Last Bit
From here on out the project goes downhill, starting with the front end of the handle.
Push the circuit through the front end of handle piece, LEDs first.
When the circuit is through push the LEDs back into the flare nut so they are not visible. Test the mess.
Use some hot glue to secure the LEDs and microcontrollers in place.
Step 27: Step 27: the Positive Battery Connection
Without a way to connect to the battery the entire project is a bust so......
Take out the positive battery connection and trim off the four corners with diagonal cutters.
There is a hole in the battery connector, put an 1 1/2 red wire though it. Solder the wire to the connector.
Ring the connector in hot glue as seen in the pictures above (if it can touch the walls of the sonic screwdriver the batteries will short out, heat up and spew acid everywhere. {or a base, since AAs use an alkaline solution}, again, doom!)
Step 28: Step 28: Batteries and Buttons
Almost there. Batteries and buttons are up.
Put the batteries in the lower handle with the bottom connector in place.
Unscrew the bottom flare nut on halfway so the spring can do it's job.
Place the battery connector made in the last step on top of the batteries in the handle, center it and hot glue it in place, making sure the hole for the button is not closed off. Test the circuit by:
screwing the bottom flare nut on entirely
connecting the red wire from the microcontroller to the one from the positive battery connector
connect the black wire from the microcontroller to the metal of the handle
it should work....
Pull the red wire from the battery connection through the button hole.
Take the free red wire from the microcontroller setup and pull it through the button hole in the same manner.
Wrap one of each of the red wires around one of the legs of the button and solder it on. Test again.
Push the button into the handle and hot glue it in place.
Test once more and the circuit is done.
Step 29: Step 29: Batteries Part 2 and Wrapping It Up
The negative battery connection is a pressure fit against the side of the handle.
Right then. Steps.
Strip some solid core wire at least 1/2 inch.
Trim that 1/2 inch of wire off.
Solder the solid core wire fragment to the black wire from the microcontroller. Push the wire fragment of solid wire along the side of the handle between it and the hot glue. Test it.
Hot glue the newest connection in place.
Screw the handle together carefully to avoid breaking wires (this is why I leave the extra length in the wires, it helps)
Test everything by making sure the batteries are in and pushing the button.
Here is where I have to pause for the night to find some more pictures and prepare for finals this next week.
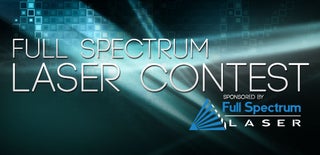
Participated in the
Full Spectrum Laser Contest